As always reference the LinuxCNC manuals and the LinuxCNC Wiki for more information.
Tool Diameter Compensation
Tool diameter compensation allows you to use different size tools for the same G code as well as provides a means to adjust the size of a part to compensate for tool wear.
Compensation Requirements
-
Lead In Move - Greater than the radius of the tool and in the X or Y.
-
Lead Out Move - Greater than the radius of the tool and in the X or Y.
-
Inside Corners - Greater than the radius of the tool.
Compensation by G code
Dynamic tool diameter compensation it done with G41.1 and G42.1.
Dynamic Tool Compensation
G20 G17 G40 G49 G64 P0.005 G80 G90 G94 (preamble) F25 (set feed rate) G0 X1 Y1 (position tool at start point) Z0.1 G41.1 D0.250 (turn on dynamic cutter comp) G3 X1 Y0.625 I0 J-0.1875 (use an arc to move to the cut position) G3 X1 Y0.625 Z0.0 I0 J0.375 (spiral down) G3 X1 Y0.625 Z-0.1 I0 J0.375 G3 X1 Y0.625 Z-0.2 I0 J0.375 G3 X1 Y0.625 Z-0.3 I0 J0.375 G3 X1 Y0.625 Z-0.4 I0 J0.375 G3 X1 Y0.625 Z-0.5 I0 J0.375 G40 (turn off cutter comp) G1 X1 Y1 (move to the exit position) G0 Z0.1 (exit out of the hole) M2
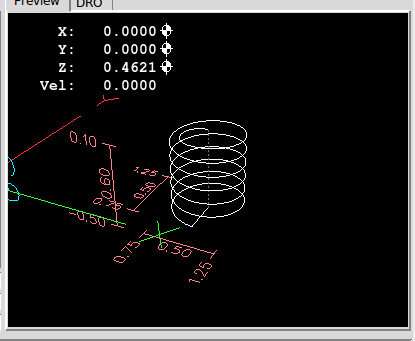
Figure 1: Spiral Backplot
This page is a work in progress…